فهرست مطالب
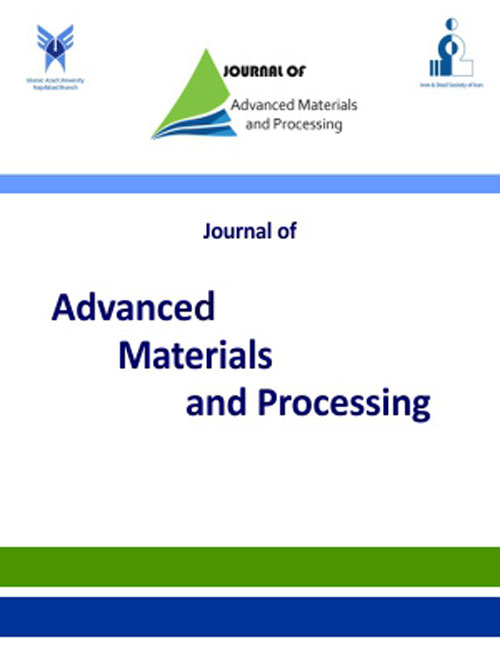
Journal of advanced materials and processing
Volume:6 Issue: 4, Autumn 2018
- تاریخ انتشار: 1397/09/10
- تعداد عناوین: 8
-
-
Pages 1-2
-
Pages 3-13
Copper is relatively soft metal and its wear and corrosion are considered to be a major factors of degradation of this metal. For this reason, when the higher wear and corrosion properties are needed, surface properties should be improved with different surface treatments. One of these methods is the applying of Ni-P electroless coating due to good mechanical properties, suitable corrosion resistance and its ability of heat treatment on Cu. In this research after the surface preparation of Cu, which included grinding, degreasing and surface activation, the specimens were dipped into commercial electroless nickel bath (SLOTONIP 70A) for 60 minutes. SEM images and the results of the EDS test confirmed the formation of Ni-P electroless coating (with 10.83 wt. % phosphorus) with a spherical structure. Applying the heat treatment increased the hardness from 495 to 880 Vickers. XRD results showed this hardening is due to the formation of Ni crystal and Ni3P phases at this temperature in the coating. The study of wear resistance and corrosion property of coatings was also done using pin-on test and polarization tests, respectively. The results showed that the heat treatment improved the wear resistance of the coating, and the weight loss in the presence of the heat treated coating reduced to 76% due to increasing hardness and roughness of the coating by performing heat treatment.
Keywords: Ni-P electroless, wear, hardness, heat treatment, polarization -
Improvement Impact Manufacturing Parameteres of Aluminum FoamsPages 12-20Lightweight aluminum foams have a wide range of industries application as good energy and acoustic absorbers. The current state of the art with regards to the production of metallic foams is reviewed, with direct foaming of Al melt processing and a CaCO3 foaming agent used to generating lower material cost, a relatively low level of impurity presence, more uniform and finer cell structures to produce semi-industrial aluminum panel foams and consequently structure properties investigated. Calcium carbonate is found to be a highly effective foaming agent for aluminium and silicon carbide used to stabilise foam structure added to the aluminum molten so led to defects elimination, which result significant reduction in the thickness of melt drainage to achieve more uniform foams. Structure properties investigated at various thicknesses and cell sizes indicated that by enhancing the thicknesses and decreasing cell sizes caused improvement of Al-foam panels. Optical microstructure(OM) and cells distribution quality of samples measured and the cell size (Dm) calculated with image analyzer by microstructural image processing (MIP) software furthermore, scanning electron microscopy (SEM) images of SiC particles to evaluate two parameters of melt drainage and foam expansion as criterions the notable fall in large cavities subsequent uniform cellular which result in desirable distribution of SiC particles on interior surface of cells. Furetheremore, Compressive deformation foams has been studied.Keywords: Aluminum foam, Foaming agent, Thickening agent, Silicon carbide, Calcium carbonate
-
Pages 21-32
Surface modification is very important in the component in industry due to wear and corrosion. In order to improve the corrosion behavior of steels, a protective coating can be deposited onto the surface. In this study Ni-TiO2 coatings were prepared on an AISI 430 stainless steel substrate by electrocodeposition process in Watt’s plating bath containing TiO2 particles. Two types of coatings was produced; without CTAB and at presence of CTAB surfactant. Isothermal oxidation behavior of uncoated and two types of coated specimens were studied up to 250 h in 800 ºC. Also cyclic oxidation was studied for 100 cycles at 800 C. Scanning electron microscope (SEM) and X-ray systems were applied in order to investigate the formed phases and structures of composite coating before and after oxidation. Results showed coated specimens at presence of CTAB surfactant had lower mass gain compared to Ni-TiO2 coated and uncoated ones after isothermal and cyclic oxidation at 800 ºC.
Keywords: Electrodepoistion, Oxidation, Ni-TiO2 coating, CTAB -
Pages 33-41
In this study, cartridge brass alloy was severely deformed by twist extrusion (TE) technique and its mechanical properties, before and after TE, was investigated using a die with the twist line slope of β = 30°. It was revealed that large strains imposed on the material by this advanced method of severe plastic deformation (SPD) led to a nano-scale ultrafine microstructure and to an enhancement of the mechanical properties. It was revealed that the more TE passes a finer grain sized microstructure obtained. Also, by increasing the number of TE passes, the yield strength and ultimate tensile strength increased. Microhardness test results show that the hardness increases from 55 (initial sample) to 110 HV and 140 HV in the center and lateral edges of the sample pass #1 TE, respectively. After six passes of twist extrusion, the microhardness of the center and lateral edges of the sample reaches 160 HV.
Keywords: Severe Plastic Deformation, Twist Extrusion (TE), Cartridge brass, Microstructure Evolution, Mechanical Properties -
Pages 42-52
In the present research porous Mg-Zn scaffolds with different Zn amount and porosities were synthesized by powder metallurgy process as potential degradable materials for orthopedic applications. The microstructures, composition, mechanical properties and in vitro biodegradability of the scaffolds were investigated. Optic microscopy (OM) images showed that the Mg-Zn scaffolds exhibit homogeneously distributed and interconnected pores with the size of about 150–400 µm. The X-ray diffractometer (XRD) results indicated the formed intermetallics consist of Mg12Zn13 and Mg51Zn20 in the Mg matrix. Compressive tests showed that decrease of porosity and the addition of Zn increases the compressive strength of specimens. Electrochemical tests indicated that with increase of porosity, the corrosion current density of scaffolds increased and Mg-Zn scaffolds synthesized improved the in vitro biodegradability property of the Mg; the best biodegradability property was obtained with 3% Zn and the porosity of about 7% ; further increase of Zn content up 4% deteriorates biodegradability. It is found that the products of immersion in simulated body fluid (SBF) are identified to be HAP, (Ca,Mg)3(PO4)2 and Mg(OH)2 and MG63 cells adhere and proliferate on the surface of the scaffolds, making them a promising choice for orthopedic application.
Keywords: Porous Scaffold, Mg-Zn, Mechanical Properties, In Vitro biodegradability, Powder Metallurgy -
Pages 53-64
The overarching goal of this research was to use the FSW method to join the Al 2024 and Al 7075 alloys, examine the structural and mechanical properties of the joint, and eventually find the optimum welding parameters. The welding operation was carried out using a milling machine and a device with cylindrical pins. The transverse cross-section of the weld was used for optical as well as electron microscopy observations. The evaluation of mechanical properties at room temperature i.e., tensile strength and hardness were done. The size of the grains measured using an optical microscope varied between approximately 2.6 and 11 µm. The results of the welding process revealed that the specimen with a traverse speed of 30 mm/min, a rotation speed of 600 rpm, and the highest ultimate tensile strength (195 MPa), and the specimen with a traverse speed of 70 mm/min, a rotation speed of 1200 rpm, and an ultimate tensile strength of 193 MPa were selected as the optimum specimens due to their off-fusion-zone failure, their high strength in the tensile strength test, and their adequate input heat. Moreover, in the specimen with the traverse speed of 100 mm/min and the rotation speed of 600 rpm, the highest percentage of elongation (3.80%) was observed in the tensile strength test. The results from the tensile test indicated that with a decrease in the traverse speed, the tensile strength of the specimens increased, the elongation percent decreased, and the stirring improved.
Keywords: Friction stir welding, Aluminum alloys, Al2024, Al7075 -
Pages 65-73
bstract: - The aim of this work was to use the electrophoretic deposition (EPD) technique for the deposition of nano-TiO2 layers directly on an SS316L substrate. The nano-TiO2 films were deposited on an SS316L alloy with various parameters, such as potential, time of deposition and annealed temperature—the optimum parameters required for the development of stable nano-TiO2 layer coating. The results obtained from the X-ray diffraction (XRD) and FESEM tests in this study showed that the TiO2 layers sintered at 400 °C were amorphous. The XRD patterns showed the anatase phase at 600 °C for 1 h. The heat treatment of TiO2 layers led to good adhesion with the SS316L alloy. The heat treatment above 500 °C led to the agglomeration of nano-TiO2 layers from 28 nm to 78 nm at 600 °C. The thickness of the nano-TiO2 coating increased with the deposition time and potential. The optimum thickness of the nano-TiO2 coating on the SS316L alloy was 50 µm at 5 min and 30 V. The increase in coating thickness with the time and potential of deposition led to problems, including increases in roughness and weak adhesion of the coating layer.
Keywords: electrophoretic deposition, titanium dioxide, SS316L